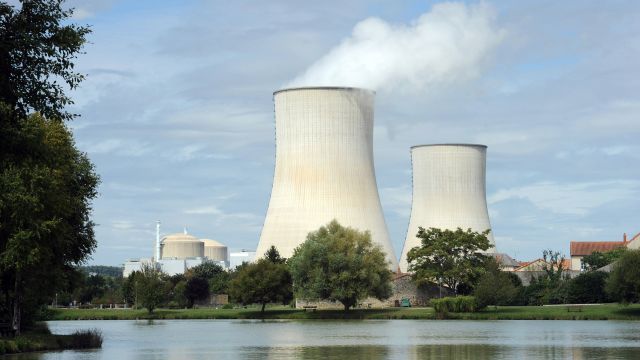
Safety-relevant damage in the safety injection systems of French nuclear power plants
The damage was first detected during the ten-yearly safety reviews of the Civaux-1 pressurised-water reactor.
Ultrasonic examinations revealed indications in the safety injection system that were attributed to cracks.
Purpose and function of the safety injection system
In the French pressurised-water reactors concerned, the safety injection system consists of a low-pressure and a medium-pressure injection system as well as the pressure accumulators.
It is connected in several places to the loops of the primary system, through which the water heated in the reactor core is fed into the steam generator and then cooled and returned to the reactor core.
The safety injection system is used to control accidents in which coolant (water) escapes from the primary system due to a leak. This accident is technically referred to as a Loss of Coolant Accident (LOCA). In such a case, water has to be injected into the primary system by means of the safety injection systems. This is necessary to supplement the loss of coolant via the leak and to ensure the cooling of the reactor core. Without this system, the so-called residual heat could otherwise not be removed, even after the reactor has been shut down, and this could lead to core damage and even core meltdown.
Safety relevance of the damage
If the cracks reach a certain size during ongoing operation, a leak or rupture of one of the affected lines may occur - especially if there is an additional mechanical load. Since there is a direct connection between the location of the crack indications and the primary system, a loss-of-coolant accident would then occur.
Scenarios are conceivable in which mechanical loads act simultaneously on all affected lines of the safety injection system, e.g. in the event of a severe earthquake. If, in such a case, several of these lines were to rupture simultaneously, core damage up to and including core meltdown could only be prevented if further emergency measures for reactor cooling could be successfully implemented.
Findings to date on the nature and cause of the damage
The pipe damage found are cracks in circumferential direction, i.e. they run transverse to the pipe direction. They are located in the base material next to weld seams. The operator has cut out affected pipe sections in order to have the cause of the damage determined by a laboratory. According to initial metallographic and microscopic examinations, the damage is due to intergranular stress corrosion cracking.
Stress corrosion cracking typically only occurs when three adverse conditions come together: high mechanical stresses, aggressive ambient conditions, and a material that is sensitive under these conditions. The exact cause of stress corrosion cracking can only be speculated at this point in time. The material concerned, a non-stabilised chromium-nickel steel, is, according to previous experience, not very sensitive to intergranular stress corrosion cracking under normal chemical conditions, i.e. practically oxygen-free hot water, in the primary system.
Effects to date and measures taken
When the damage found at the Civaux-1 plant became known, the operator also took Unit 2 off the grid for investigations; the Chooz B-1 and B-2 reactors, which are of an identical design, were also shut down - this means that all N4 reactor units, the most powerful French reactors with a gross rating of 1560 MW, are off the grid.
In addition, cracks were also found during overall maintenance inspection work in the safety injection system at the Penly nuclear power plant. This is a P'4-type reactor; however, the crack indications found there are not as pronounced as those in the N4 reactors. At the present time, it cannot be ruled out that further plants of this type will have to be examined in the short term. In France, a total of twelve of these reactor units are operated at five different locations.
EDF is currently still carrying out in-depth investigations on the cut-out pipeline sections. At the same time, the manufacturing documents are being evaluated, operating conditions are being analysed, and tests carried out so far are being re-examined for any indications. The investigations, the repair work and the inspections by the supervisory authorities and expert organisations will in any case take several months.
Update 03 August 2022
All reactors to be checked by 2025
In the meantime, the French nuclear supervisory authority ASN has examined the inspection strategy proposed by the operator EDF and assessed it as appropriate. The strategy provides for EDF to inspect all its reactors for damage by 2025, using a new, non-destructive ultrasound testing procedure. This procedure was developed with the aim of reliably detecting cracks caused by stress corrosion cracking and estimating their depth.
EDF had carried out a great deal of work in recent weeks and months to deepen the understanding of the corrosion phenomenon and identify the affected areas. Among other things, this involved 70 laboratory examinations of material from the vicinity of welds from a total of eight reactors. Here, the geometry of the pipes and their thermomechanical loads were identified as the main causes of the occurrence of stress corrosion cracking.
According to EDF, the following are particularly susceptible to the corrosion phenomenon
- the safety injection system lines located in the cold leg and the suction lines of the residual-heat removal system of the N4-type reactors (two 1,450 MW units each at Chooz B and Civaux);
- the safety injection system lines located in the cold leg of the P'4-type reactors (a total of twelve 1,300 MW units at the Belleville, Cattenom, Golfech, Nogent-sur-Seine and Penly sites).
The corresponding systems of the P4-type reactors (1,300 MW) and the 900 MW reactors are only barely susceptible to this form of stress corrosion cracking according to the current state of knowledge. The inspection strategy therefore envisages prioritising the N4 and P'4-type reactors. The new inspection method is to be applied for the first time in the second half of 2022.
Applicability to German nuclear power plants
On behalf of the Federal Environment Ministry, GRS is monitoring the situation in France and is also looking at a possible applicability to German nuclear power plants on the basis of the information available. According to the current state of knowledge, it is assumed that this is not the case, which is confirmed by the test results available: The German plants are regularly inspected using suitable procedures to detect the occurrence of damage to the components at an early stage. So far, no cracks of this kind have been detected during these inspections.